Table of Content
- Europe’s Defense Boom: The Impact on a Supplier of Metalworking Products
- Rising Demand for Metals: The Strain on Natural Titanium and Steel Supply
- How Army Armament is Putting Pressure on Global Supplies Beyond Metals
- Metalworking Supply Chains: Managing Geopolitical Risks and Stock Control
- Pro Tip for a Supplier of Metallurgy: Diversify and Strengthen Strategic Partnerships
- Resource Competition: How Civil Industries and Army Armament Are Battling for Supplies
- Adapting to Change: Smart Strategies for a Supplier of Metalworking Products
- Boosting Production Chains with Smart Technology and Innovation
- Key Trends and Insights: Production Chain Developments in Europe’s Steel Market
- Conclusion
1. Europe’s Defense Boom: The Impact on a Supplier of Metalworking Products
The rapid expansion of army armament across Europe in 2025 is changing how resources are distributed. Many countries are working to meet or surpass NATO’s 2% GDP defense spending target, with some going even further.
Take Germany, for example—it has allocated a massive €100 billion for military upgrades, while France, Poland, and the Baltic states are also ramping up their defense budgets. This surge in investment is fueling procurement, research, development, and infrastructure improvements, injecting billions into the defense sector.
For a supplier of metallurgy, this shift has major consequences. The sheer volume of steel needed for tanks or natural titanium for fighter jets highlights the scale of demand for army armament. And this isn’t just a temporary spike but a long-term shift that will reshape the industry for years to come.
Companies that rely on a steady metal supply are already feeling the impact. Supplier shortages, stock control, and production chain slowdowns are becoming more common. To stay ahead, every supplier of metalworking products must adapt to this rapidly evolving landscape.
In this challenging time, as supply chain disruptions, geopolitical tensions and, and rising costs are impacting the industry, finding the right supplier of metallurgy is crucial for any business. Explore europages’ listing dedicated to suppliers of metalworking products.
2. Rising Demand for Metals: The Strain on Natural Titanium and Steel Supply
For a supplier of metalworking products, staying informed about the shifting demand for essential materials is crucial to navigating today’s challenges. Understanding which metals are in high demand—and how they impact business—is key to staying competitive.
Among these critical materials, natural titanium stands out as one of the most vital for modern military equipment.
Natural titanium plays a crucial role in modern defense, thanks to its exceptional strength-to-weight ratio and resistance to corrosion. It’s a key material in aerospace applications, used in fighter jets, missiles, helicopters, naval vessels, and armor plating.
Russia has long been a major supplier, but ongoing conflicts and sanctions have disrupted the flow, creating immediate vulnerabilities.
Beyond titanium, rare earth elements are another growing concern. These materials are essential for high-performance magnets used in advanced electronics, guidance systems, and electric motors—critical components in military drones and electric vehicles.
The challenge? China dominates the rare earth market, controlling both mining and processing, making supply chains highly vulnerable to geopolitical tensions and price fluctuations.
Steel is also feeling the pressure, particularly specialized alloys used in armor plating and weapons systems. These high-strength materials rely on elements like nickel, chromium, and molybdenum, which come with their own supply risks.
For every supplier of metallurgy, these shortages are already having a ripple effect. Longer lead times, rising costs, and the need for smarter stock management are becoming the new reality. To stay ahead, companies must take a strategic approach to sourcing and inventory control to navigate these evolving challenges.
-1065x562.jpg)
3. How Army Armament is Putting Pressure on Global Supplies Beyond Metals
The surge in military spending isn’t just impacting metals—it’s putting pressure on a wide range of essential materials. For a supplier of metallurgy, the strain is becoming more apparent as defense programs ramp up their demand for critical resources.
Engineering polymers and plastics, used in protective gear, military vehicles, and aerospace components, are now in higher demand. Specialty chemicals, essential for explosives, propellants, and protective coatings, are also seeing supply constraints.
However, one of the biggest concerns is the semiconductor shortage. Already disrupting industries worldwide, this crisis is set to deepen as army armaments compete for advanced chips.
From communication systems and radar to weaponry and sensors, modern defense technology relies heavily on semiconductors. As demand outpaces supply, delays and rising costs will ripple through multiple industries—including those outside the defense sector.
This competition for limited semiconductor supplies creates a ripple effect, potentially delaying production and driving up costs in many industries, even those not directly involved in defense.
Because supply chains are so interconnected, a shortage in one area can quickly trigger disruptions elsewhere. With many critical materials in limited supply and global conditions shifting rapidly, industries across the board are feeling the squeeze.
For a supplier of metalworking products, this adds another layer of complexity. The big question now is: Can companies mitigate risks by sourcing alternative materials, or will industries need to rethink product designs to adapt to a strained supply chain?
4. Metalworking Supply Chains: Managing Geopolitical Risks and Stock Control
The current geopolitical climate is making supply chains more unpredictable, including every supplier of metalworking products who rely on specific countries for critical raw materials.
This dependence brings risks that go beyond basic supply and demand. Political tensions, trade restrictions, and conflicts can disrupt the flow of essential materials, leading to shortages, production delays, and rising costs. Sanctions, export bans, and shifting alliances now play a major role in determining how and where businesses can source their materials.
To stay ahead, every supplier of metallurgy must take a proactive approach to risk management. It’s no longer just about ensuring materials are available—it’s about evaluating geopolitical stability, transportation challenges, and alternative sourcing options.
Companies that prepare for these uncertainties through strategic stock control and supplier diversification will be in a stronger position to maintain steady production. In today’s volatile market, building a resilient supply chain isn’t just a smart move—it’s essential for long-term success.
Are you looking for a supplier of metalworking products with a resilient and diversified supply chain? Request a free quote on europages to find the ideal supplier.
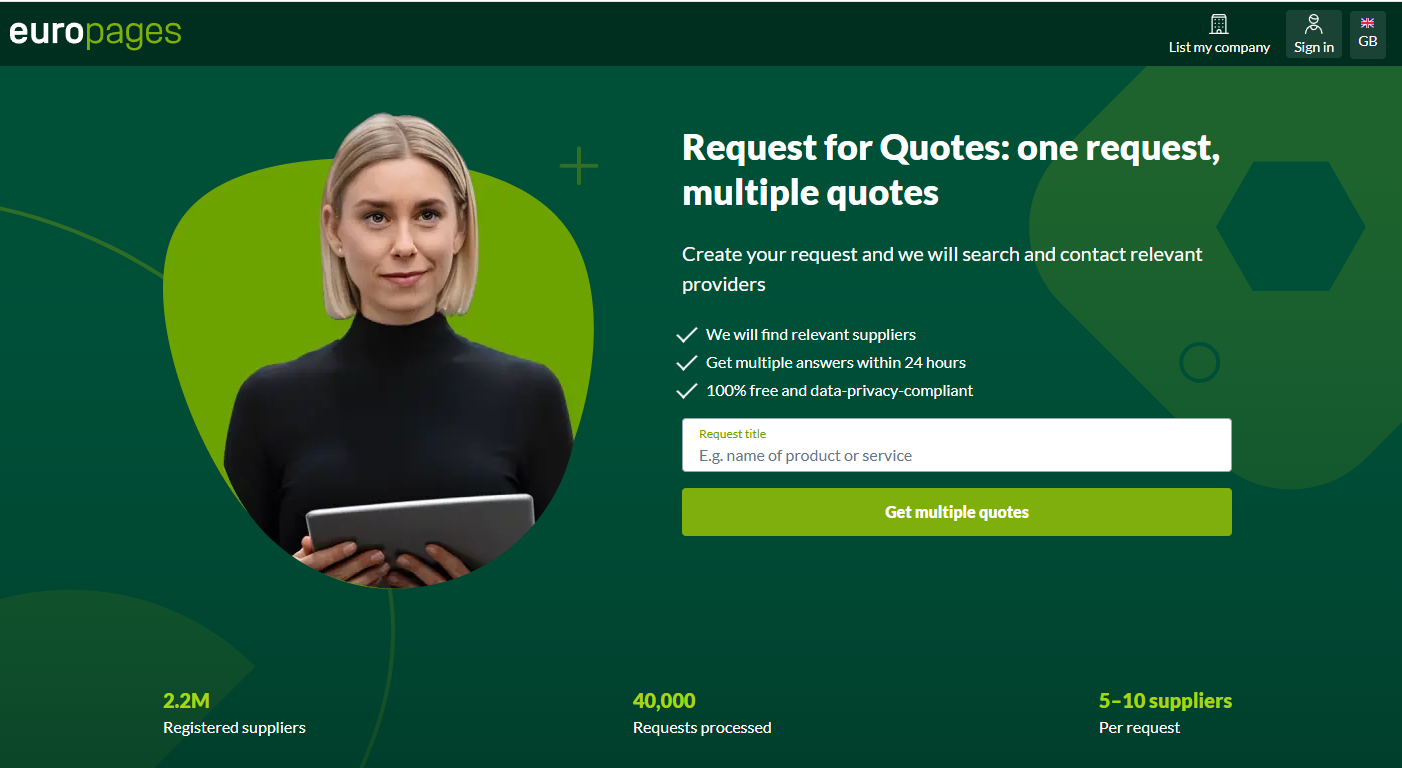
5. Pro Tip for a Supplier of Metallurgy: Diversify and Strengthen Strategic Partnerships
Businesses can safeguard their production chains by diversifying their sources of raw materials.
Relying on a supplier of metalworking products, especially from politically unstable regions, can leave companies vulnerable to disruptions. Securing alternative sources for critical materials like natural titanium helps reduce these risks.
While qualifying new suppliers can be time-consuming and costly upfront, it’s a crucial step for maintaining effective stock control and ensuring long-term resilience.
Beyond just finding a new supplier of metallurgy, building strong, strategic partnerships is key. Open communication, joint planning, and shared investments turn one-time transactions into long-term, stable business relationships.
The European Commission also underscores the importance of diversifying country supplies, particularly for industries like defense, to prevent resource shortages and supply chain breakdowns.
Taking a proactive approach allows a supplier of metalworking products to better navigate uncertainties and maintain steady production.
6. Resource Competition: How Civil Industries and Army Armament Are Battling for Supplies
The rising demand from army armament is putting immense pressure on suppliers of metallurgy, making it harder for civil industries to access the materials they need. As military orders surge, resources become more limited, creating direct competition between defense contractors and non-military businesses.
In Europe, defense companies often receive priority access to critical materials like natural titanium due to government policies focused on national security.
This leaves B2B companies in sectors like automotive, construction, and manufacturing struggling to secure supplies, facing higher prices, stock shortages, and longer lead times—all of which disrupt production chain schedules and profitability.
Smaller businesses are hit the hardest. With less buying power and weaker supplier relationships than major defense contractors, they often find themselves at a disadvantage when competing for scarce resources.
So how can civil industries stay competitive when the defense sector gets top priority? Finding ways to ensure fair access to materials—whether through diversification, strategic partnerships, or advocacy for balanced country supplies—has become a crucial challenge for every supplier of metalworking products looking to maintain stability in an increasingly competitive market.
7. Adapting to Change: Smart Strategies for a Supplier of Metalworking Products
To navigate supply chain disruptions and stay competitive, a supplier of metalworking products needs to go beyond just diversifying their business partners and forming strategic collaborations.
Here are some key strategies to strengthen resilience and keep production chains running smoothly:
Smart Inventory Management
Investing in modern inventory systems can help improve stock control and reduce unexpected shortages. Key steps include:
- Using accurate forecasting models to predict demand fluctuations.
- Leveraging data analytics to anticipate shifts, especially in sectors like army armament.
- Maintaining safety stock of critical materials to buffer against supply disruptions.
Exploring Material Alternatives
Look for alternative materials that can replace scarce resources. For example, aerospace companies are turning to advanced composites and aluminum-lithium alloys instead of natural titanium, helping to reduce dependence on limited country supplies.
Circular Economy Practices
Recycling and reusing materials can help reduce dependence on newly mined resources. Practical steps include:
- Designing products that are easier to disassemble and recycle.
- Investing in recycling technologies to recover valuable materials.
- Partnering with recycling businesses to create a more sustainable supply chain.
Collaborating with Industry Peers
Engaging with trade associations and industry groups can provide valuable insights, strengthen negotiating power, and create opportunities for collective problem-solving.
Regular Contract Reviews
Frequently evaluating supplier agreements—especially with partners in different regions—can help businesses anticipate risks, avoid conflicts, and ensure smoother operations.
For a supplier of metalworking products, adapting to today’s challenges requires a combination of strategic planning, flexibility, and proactive decision-making.
8. Boosting Production Chains with Smart Technology and Innovation
While short-term solutions help manage immediate challenges, the long-term success for every supplier of metallurgy may rely on technological innovation.
Investing in research and development can open new doors, leading to the discovery of alternative materials, improved manufacturing techniques, and more sustainable sources of critical resources.
Here are some game-changing technologies that could transform the industry:
Additive Manufacturing (3D printing):
Helps minimize material waste and enables the creation of intricate components without being overly dependent on traditional machining techniques.
Unconventional Resource Extraction:
Exploring innovative methods to extract critical metals from unexpected sources, such as mining waste or even seawater.
New Material Development:
Developing new alloys and composite materials that lessen reliance on hard-to-find critical metals.
How can B2B companies, including suppliers of metalworking products, take advantage of these technological advancements and play an active role in shaping the future of the industry? Finding the answer to this could be the key to long-term success and staying competitive in a rapidly evolving market.
Are you a supplier of metallurgy looking for more exposure and reach? Request a consultation with our team to explore partnership opportunities.
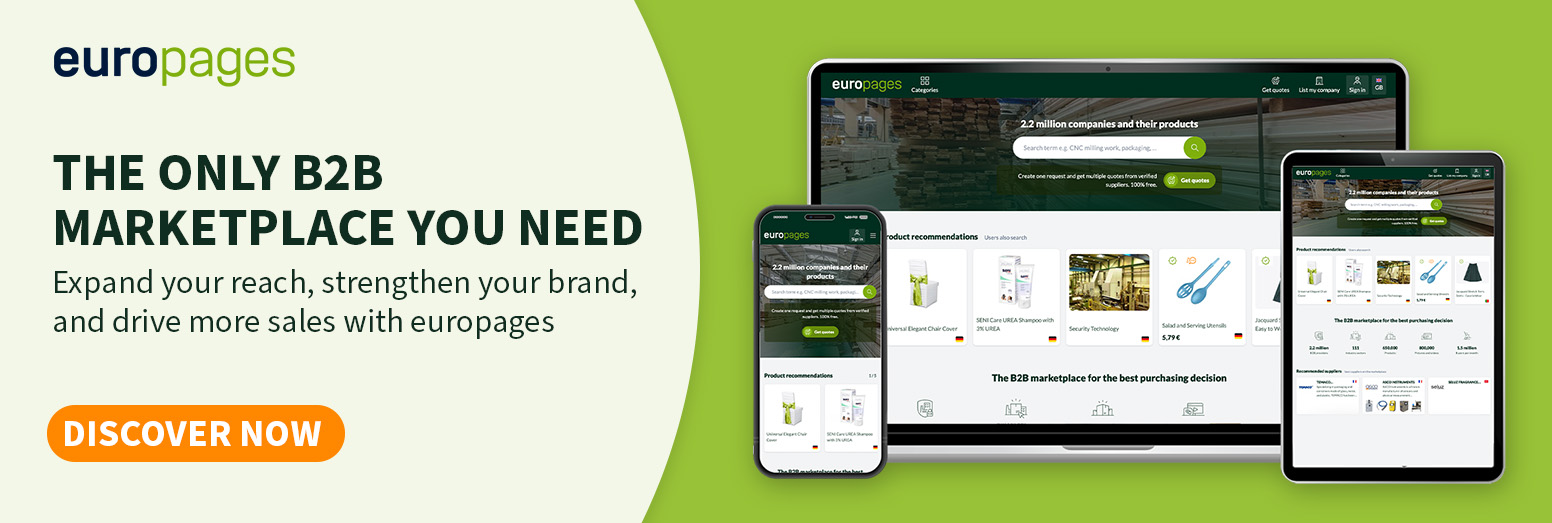
9. Key Trends and Insights: Production Chain Developments in Europe’s Steel Market
Steel is the backbone of key industries like automotive, construction, and defense, making Europe’s steel market a vital part of the region’s economy. In 2024, the EU produced around 136 million metric tons of steel, with Germany, Italy, France, Spain, and Poland leading production.
The recent rice in army armament, especially Germany’s €100 billion investment in defense, has significantly increased demand for specialized steels used in military vehicles and armor plating. As a result, prices for these high-performance materials have jumped 15–25% since 2023, driven by rising demand and supply chain pressures.
To keep up with demand, Europe imported approximately 23 million metric tons of steel in 2024, primarily from Turkey, India, South Korea, and China. However, with growing geopolitical uncertainties, there is a strong push to reduce reliance on imports by strengthening domestic production and diversifying supply sources.
At the same time, sustainability is becoming a top priority. The EU’s "Fit for 55" plan is accelerating efforts to make steel production greener through hydrogen-based processes, increased recycling, and carbon capture technologies—all aimed at cutting emissions by 2030.
As Europe’s steel industry faces the dual challenge of meeting rising military needs while advancing environmental goals, suppliers of metalworking products must adapt, innovate, and build more resilient supply chains to stay ahead in this evolving market.
10. Conclusion
Europe’s increasing defense spending, combined with ongoing global supply chain vulnerabilities, presents a major challenge for every supplier of metalworking products.
The demand for essential materials like natural titanium, steel, and rare earth elements is skyrocketing, leading to fierce competition, rising costs, and concerns over potential shortages.
For every supplier of metallurgy, this means navigating geopolitical risks, diversifying sourcing strategies, strengthening partnerships, and implementing smarter inventory management practices to stay ahead. But addressing these immediate concerns is only part of the equation.
The bigger issue looming on the horizon is resource scarcity. The traditional "take, make, dispose" approach to materials is becoming unsustainable, especially as global demand continues to grow. Simply securing raw materials won’t be enough; industries must rethink how they use and reuse resources.
A shift toward circular economy principles—designing products to last longer, making them easier to disassemble, and improving recycling efficiency—will be key.
Investing in closed-loop systems and advanced recycling technologies to recover valuable metals from complex products will be crucial in reducing dependency on newly mined materials.
This transformation requires collaboration across industries, governments, and consumers. While the shift toward sustainability presents significant challenges, it also brings opportunities for innovation and long-term resilience—not just for the metalworking sector, but for the entire industrial landscape.