Precise Machining Technology through Computerized Control
CNC (Computerized Numerical Control) milling is a high-precision manufacturing process in machining and forming in which workpieces are brought into the desired shape using a rotating milling tool. At the heart of this technology is the computer numerical control (CNC). A detailed 3D model of the workpiece serves as a digital template.
This 3D model is translated into a CNC program that defines the exact motion sequences of the milling tool. The CNC machine then executes these instructions precisely by moving the tool along the specified paths to remove the excessive material.
The high precision is achieved through a combination of powerful hardware and intelligent software. Feedback systems ensure that the actual movements of the tool are continuously compared with the target values in order to minimize deviations.
The Components of a CNC Milling Machine and how they work
To ensure high-level precision and flexibility of CNC milling processes, CNC machines are equipped with a variety of components. Each component plays a crucial role in converting digital data into physical precision parts.
One important component is the machine bed. It forms the foundation of the machine and supports all moving parts. It must be extremely stable to minimize vibrations during the milling process and ensure precision.
The axes of the machine move the workpiece or tool along the X, Y and Z axes. High-precision linear guides ensure smooth and accurate movement.
At the same time, the spindle holds the milling tool and rotates it at high speed. The speed can be adjusted depending on the material and machining process.
For complex components, it is often necessary to use different milling tools. A tool changer enables the tools to be changed automatically during the machining process.
However, the center of the machine is the CNC control. It processes the digital data from the CAD model, calculates the tool paths and controls the movement of the axes and the spindle
The Role of CNC Milling in the Aerospace Industry
CNC milling machines have proven to be indispensable in the aerospace industry. They enable the production of precision parts that can hardly be achieved in any other manufacturing process. This high-precision machining technology is crucial for the production of components that have to withstand extreme loads and at the same time have a low weight.
Why is CNC so important for the aerospace industry?
- Precision parts at the highest level: CNC machines can produce components with extremely tight tolerances, which is essential for the functioning of complex systems such as engines or avionics.
- Complex geometries: Computerized control enables the production of components with almost any shape, from simple cylinders to complex organic structures.
- Repeatability: Each part produced by CNC is almost identical to the previous one. This is particularly important for series production and ensuring quality.
- Versatile material processing: CNC machines can process a wide range of materials, from light metals such as aluminum and titanium to high-strength special alloys.
- Flexibility: By simply changing the CNC program, prototypes can be produced quickly or production can be switched to new components.
- Automation: Many processes can be automated, resulting in higher productivity and cost efficiency.
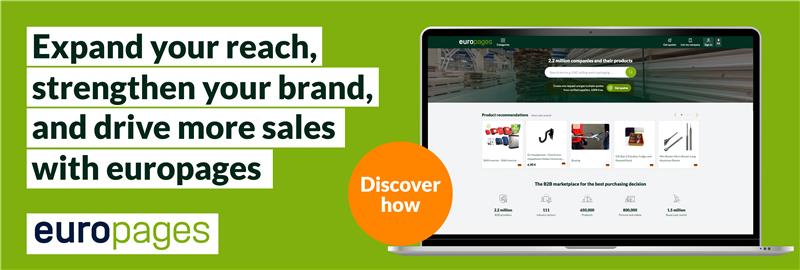
Examples of CNC Milling Processes in the Aerospace Industry
CNC milling processes are used in the aerospace industry for a variety of applications. One example is the manufacturing of engine components. These components must withstand extreme temperatures and pressures. By using CNC milling processes, high-precision and durable engine components can be manufactured.
Another example is the production of aircraft fuselages. These components have to be light yet stable. By using composite materials and CNC milling processes, aircraft fuselages can be manufactured with optimum weight distribution and high rigidity.
Economic Advantages of Machining Technology in the Aerospace Industry
CNC milling processes offer numerous economic advantages for the aerospace industry. The high level of automation and precision of these machines can reduce production costs and increase the quality of components. The flexible adaptation to new requirements and the reduction of material waste also contributes to efficiency.
In addition, CNC machines enable the production of complex components and support the development of new business models. Overall, CNC milling processes increase the competitiveness of companies in the aerospace industry and contribute to the efficient and sustainable production of precision parts.
The Importance of CNC Milling for Green Aerospace
CNC milling has established itself as a key technology in the aerospace industry. However, the importance of this technology goes far beyond the production of complex components. By precisely removing material and avoiding waste, CNC milling makes a significant contribution to conserving resources.
The use of lightweight materials, which can be specifically machined thanks to CNC machines, reduces the weight of air- and spacecraft and thus lowers fuel consumption. In addition, modern CNC machines allow the processing of recycled materials and the use of energy-efficient processes. The digitalization of production, which plays a central role in CNC milling, optimizes logistics processes and reduces transport routes.
By combining these factors, CNC milling makes an important contribution to sustainability in the aerospace industry and supports the development of environmentally friendly air- and spacecraft.
Challenges and Solutions in the Aerospace Industry
However, the aerospace industry also places high demands on the reliability and safety of components. In order to meet these requirements, machining techniques and the tools used must be continuously developed.
One important challenge is the machining of high-strength materials such as titanium alloys. Although these materials are very robust, they are also difficult to machine. However, efficient machining can be achieved by using special milling tools and cooling lubricants.
Another challenge is maintaining strict tolerances. To meet these requirements, CNC machines must be equipped with high precision. In addition, the tools must be checked and calibrated regularly. Predictive maintenance could be the right solution for this problem.
Unlimited Potential of CNC Milling and AI
CNC milling processes play a crucial role in the production of precision parts for the aerospace industry. By combining state-of-the-art machining technology and high-quality tools, complex and high-precision components can be manufactured.
But the maximum potential of CNC milling is far from exhausted. By combining machining technologies and artificial intelligence (AI), it is possible to achieve a level of precision and efficiency in the aerospace industry that has never been seen before.
Whether AI can prevail in the aerospace industry remains to be seen. However, the potential behind the interaction of the technologies can be acknowledged with a clear conscience.
Find Metal Parts Suppliers that work with CNC Machines for Your Project:
PM PERA METAL SAN.TIC.LTD.STI.: Pera Metal is a metal processing company that specializes in CNC machining and offers a range of services, from raw material supply to finished products, serving various industries including construction and automotive.
SHENZHEN PROMOSTAR HARDWARE CO.,LTD: ShenZhen PromoStar Hardware Co., Ltd. is a CNC metal processing company specializing in turning, milling, stamping, and welding for various industries, offering high-precision products with tight tolerances and meeting international standards, with a focus on customer satisfaction and long-term team collaboration.
MECALTEX MECANICA GERAL DE PRECISÃO LDA: MECALTEX is a Portuguese company specializing in precision mechanics and subcontracting services for the European market since 1996.
ANDREAS BERG STAHL- UND MASCHINENBAU E.K.: Berg Stahl-und Maschinenbau e.K., a family-owned company with over 40 years of experience, provides a wide range of services, from cryogenic processing and 3D printing to steel construction and welding, offering high-quality solutions for various industries worldwide.
TEKNOMECCANICA: Teknomeccanica S.r.l., an Italian company with over 30 years of experience in precision mechanical processing, utilizes cutting-edge technology and focuses on customer satisfaction by delivering high-quality products at competitive prices.